The next time tells you we don’t make anything anymore in the USA; invite them to a take a foundry tour.
What gets measured gets done.
— Tom Peters
A foundry is a factory that produces metal castings. Metals are cast into shapes by melting them into a liquid, pouring the metal in a mold, and removing the mold material or casting after the metal has solidified as it cools. The most common metals processed are aluminum and cast iron. However, other metals, such as bronze, brass, steel, magnesium, and zinc, are also used to produce castings in foundries.
Things that Get Measured – Get Done!
The last few weeks the Team has been working in foundries. Aluminum and iron foundries which produce tons of parts for industries around the globe, the Team was working to help solve problems.
Any good problem solving exercise starts with a few vital steps:
· First Step in Solving any problem is admitting there is a problem
· Develop a baseline
“Problem solving consists of using generic or ad hoc methods, in an orderly manner, for finding solutions to problems. Some of the problem-solving techniques developed and used in artificial intelligence, computer science, engineering, mathematics, medicine, etc. are related to mental problem-solving techniques studied in psychology.” a “baseline” is an agreed description of the attributes of a product, at a point in time, which serves as a basis for defining change. We need to know where we are, how the process performs.
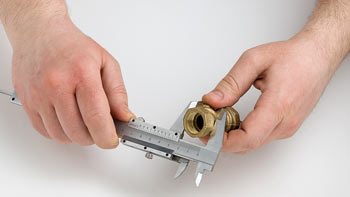
Just as measurement of a physical product is an important party of quality management, so is the measurement of countless factors that impact the entire process.
An often overlooked action in problem solving is the system is the discipline to understand it will take time. Clayton M. Christensen is an author and a professor at the Harvard Business School. Part of the curriculum at HBS is to teach MBA students to ask and understand, what causes what and why. What causes what and why is the analysis piece. Often called root cause analysis-RCA.
A root cause analysis identifies the set of multiple causes that together might create a potential accident or incident. Root causes techniques most notably the tree structure from Fault Tree Analysis, which was originally an engineering technique. The root cause analysis techniques can be categorized into two groups: a) tree techniques, and b) check list methods. There are several root causal analysis techniques, e.g. Management Oversight and Risk Tree (MORT) analysis. Others are Event and Causal Factor Analysis (ECFA), Multi linear Events Sequencing, Sequentially Timed Events Plotting Procedure, Savannah River Plant Root Cause Analysis System.
Many teams struggle with Problem Solving and Root Cause Analysis because they think one and done; Problem solving and Root Cause Analysis iterative process and a tool of continuous improvement.
Family Businesses need to use problem solving tools. Tom Peters in his book In Search of Excellence states “What gets measured gets done.” Family Businesses need metrics and problem solving tools. Family owned foundries understand process control and systems. Operational Improvements must be linked to Organizational Development.
The first step in solving any problem is …
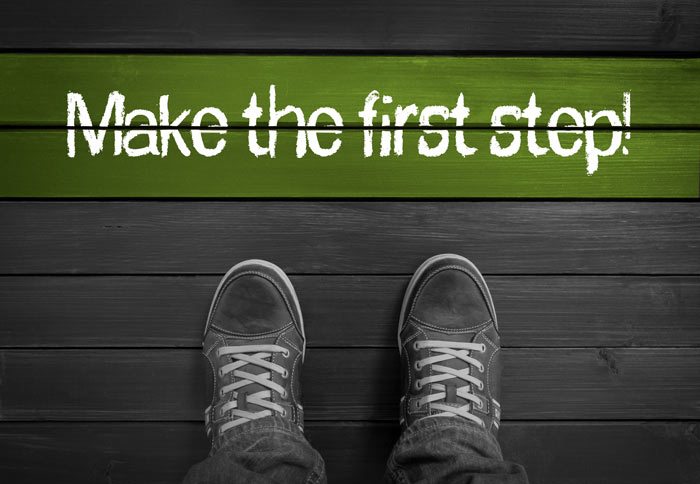
“What gets measured gets done” … make the first step!
What gets measured, gets done! That is so true. The way to know if something you have done was successful